关闭视频
/
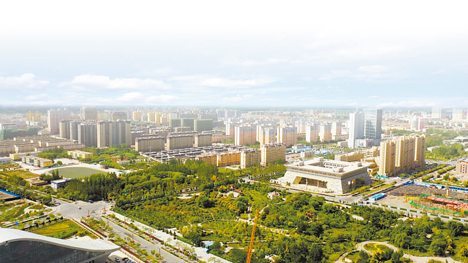
库车古城的保护利用
作为新疆维吾尔自治区延续时间最长、历史文化遗产类型最为丰富的历史文化名城之一,库车被称为“露天博物馆”。通过实施“拯救老屋行动”、建设龟兹博物馆、建成并开放国家历史文化名城展示中心等举措,库车正在成为融合历史人文与现代气息、充满生机与活力的历史文化名城样本。
中国优质产能,让全球发展受益
中国新能源产能非但没有威胁他国产业发展、冲击世界经济,还在持续为全球绿色发展作贡献。
火爆的奥运订单 绕不开的中国制造
一次次重大赛事,义乌缘何总能抓住商机、赢得市场青睐?
“希腊有充分理由支持高质量共建‘一带一路’”
“希腊和中国的文明交流互鉴超越了双边范畴,具有世界意义。”
台湾知名作词人方文山:让传统文化更流行
多年来,无论是创作中国风歌词,还是尝试跨界艺术,方文山都是想让传统文化变得更加流行。
查看更多深度评论- 汇民智
- 解民忧
- 30天回复率排行
- 聚焦网上群众路线 (回复率:留言中被回复的数量占留言数的百分比)